Dimensjonering av transportanlegg ved hjelp av luft
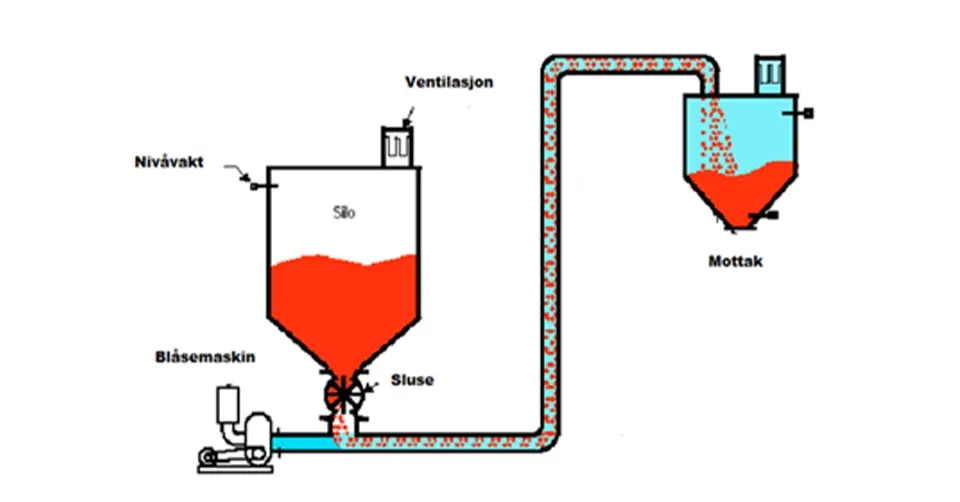
En mye brukt metode for å transportere pulvermateriale mellom to eller flere steder er ved å
benytte luft. En rørgate kan legges der det passer best, langs vegg, under tak eller mellom to
bygninger. Materialet mates inn ved startpunktet og blander seg med luften, i enden så skjer
det motsatte, materialet samles opp i en mottaker mens luften ledes ut.
Trykk
kapasitet målt i kg/min, hvor rørgate ønskes plassert, om det er inne eller ute eller i en
kombinasjon og hvor mange bend det blir. Vi ønsker også å vite hvordan materialet tenkes
matet inn og hvordan det ser ut i enden, skal det inn i en silo eller skilles det ut i en syklon. Vi
må ha data på materialet definert som partikkelstørrelse, bulk / partikkelvekt og om det er
spesielle egenskaper vi må ta hensyn til. Tåler det varme, skal det ikke knuses eller er det
følsomt for fukt.
Før vi beregner videre så må vi først definere hvor stor indre diameter rørgaten skal ha.
Denne må vi i begynnelsen velge ut ifra erfaring. Om vi ikke velger riktig så må regnestykket
under gjøres på nytt. Vi definerer det som riktig om trykkfallet og blandingsforhold (laderate)
ligger på ønsket nivå. Vi ønsker å transportere materialet i en slik blanding at det flyr i
rørgaten. For å gjøre det så må vi først bestemme hvor stor starthastigheten skal være.
Luften blåses inn i røret samtidig som at materialet ledes inn. Vi sier at laderaten skal være
maks 10 kilo materiale per kg luft. Ved atmosfærisk trykk og ved 20 0 C så vil det si per 833
liter. Et blandingsforhold over dette vil gjøre tettheten større og føre til at materialet vil kunne
falle ned i bunn av rørgate og skyves av gårde. I ytterste fall så kan det lede til tetting om vi
ikke aksepterer en større lufthastighet og tilsvarende trykkfall. I fasen vi beskriver her så
ønskes ikke det. Vi vil holde oss under eller opptil 1 bar.
For å finne starthastigheten så definerer vi hvilken hastighet ønsket mengde materialet må
ha for å fly i et vannrett rør. Vi benytter en formelmengde som ender akkurat i den
hastigheten luften har når partikkelen, pelleten etc ramler ut av luftbanen og legger seg i
bunn. Så legger vi til en prosentsats mengde luft over denne verdien.
Det er slik at trykket i en blåsetransport er størst på startpunktet, utover blir det lavere og
ender til slutt i atmosfærisk trykk. Videre så retter forholdet mellom trykk, volum og
temperatur seg etter formelen (P1 x V1) / T1 = (P2 x V2)/T2. P = Trykk, V = Volum T =
temperatur. Venstre siden av formelen er innsugstrykk der blåser står, volumet og
temperaturen på luften blåseren suger inn. Venstre side er situasjonen i røret der vi ønsker å
måle det. Og vi ønsker å måle det på det punktet der materialet ledes inn. For å måle
hastigheten så benytter vi formelen m/sek = volum per sek/areal. Arealet gis av rørgaten vi
har valgt, volum per sekund beregner vi ut ifra hva blåseren har sugd inn. I utgangspunktet
så ønsker vi å finne den minste rørgaten som kan benyttes i forhold til riktig laderate og
trykkfall. Jo mindre areal vi benytter på røret, jo mindre luft trenger vi – som igjen betyr at vi
kan benytte mindre kilowatt for å transportere. Beregningen må ofte gjøres mange ganger for
å finne den riktige blandingen mellom trykkfall og laderate.
Høyt trykk i et pneumatisk transportsystem har også en annen bakdel. Om vi starter på 20
m/sek så vil hastigheten i enden være mye større, kanskje rundt 35. Om vi ikke ønsker så
stor hastighet så har vi en mulighet til å øke rørdimensjon nærmere enden. Vi kaller det å
«steppe opp» røret. Hvor det skal steppes må beregnes da hastigheten ikke må bli så lav at
den fører til tetting. Vi må være sikre på at partikkelen vil fly i den neste størrelsen.
På mottaket så kan vi lede rørgate rett inn i en silo eller vi kan benytte en syklonutskiller som
separer luft og materiale. Luften går ut i topp og materialet ledes ned i silo via en slusemater,
dvs en roterende enhet som fjerner det som komme inn samtidig som nytt ankommer. Ledes materialet direkte inn i silo så vil denne ha et filter på toppen som leder ut luften. I og med at
en silo har et ganske stort areale så blir hastigheten så lav at partiklene ramler ned av seg
selv. Luften/materialet kan også ledes inn tangentialt, det føres inn langs silovegg som igjen
bremser hastigheten så mye at materialet faller ned. Luften vil presses ut gjennom filteret på
toppen.
Når det gjelder bend så er det viktig at disse ikke plasseres for nært hverandre. Materialet vil
presses ut mot rørveggen og miste fart før det får opp hastigheten igjen i neste rette strekke.
Om avstanden til et nytt bend er for liten så vil ikke hastigheten rekke å komme til riktig nivå
før neste brems. Da kan vi oppleve tetting. Hvor langt det bør være mellom bendene er et lite
regnestykke. Som fingerregel så kan vi benytte mellom 1,5 og 2 meter. Lengden på bendene
velges etter hvilket materiale vi transporterer. Lange bend defineres som lik eller større
radius enn 12-15 ganger indre diameter, korte kan ha en radius med tilsvarende verdi på 2.
Det finnes også såkalte slitasjebend, de er utformet med belegg i ytre gli-flate eller har
innordning som reduserer slitasjen. På den måten så kan korte bend velges om
installasjonen forlanger det.
Hvor bendene plasseres i rørstrekket bør også tenkes på. Ideelt sett så er tankegangen at
traséen bør være så rett som mulig. Må en benytte bend så er det best å plassere de så
nært startpunktet som mulig. Det har med lufthastighet å gjøre, på starten er denne lavest.
Og lavest lufthastighet gir lavest trykkfall. En annen sak er at når hastigheten går opp så blir
det også større slitasje.
Rørgater må alltid monteres vannrett eller loddrett. Vi må om mulig ikke benytte skråstilte rør.
I skråstilte gater så vil materialet ha en tendens til å legge seg i bunn, det blir tatt igjen av nytt
materiale som igjen danner «dyner». Når «dynene» legger seg i bunn så vil luften som
passerer får mindre overflate å fly i og av den grunn øker hastigheten. Til slutt får luften tak
og materialet vil «skyte» opp røret. En måte å unngå at det danner seg «dyner» er å
opprettholde for stor fart på luften. Men det er noe vi helst ønsker å unngå grunnet slitasjen
og økt kilowattforbruk.
Valg av type rørgate er viktig. Er røret utendørs bør det tåle vær, er det et langt strekke så er
det smart å finne et med lav friksjon. All motstand vil kreve mere kraft fra blåseren. Friksjon
sliter også på det som skal fly, vi ønsker denne redusert så mye som mulig.
Det kan skille seg ut fukt i rørgaten om forholdene tilsier det. Vi presser mye luft inn og
trykket øker. Kompresjonen som oppstår øker temperaturen og luften vil kunne inneholde
mye fukt i dampform. Ledes røret til et kaldere sted så vil temperaturen inne i røret også
synke. Og da kan det gå så lavt at det skilles ut vann. Om røret f. eks går mellom to
bygninger så vil det være smart å isolere det. En annen metode kan være å sette på en
varmeveksler rett etter blåser, veksleren kjøler ned luften og vi får fjernet dråpene før de
kommer i kontakt med materialet.
Uansett hvordan anlegget skal se ut så er det viktig å gå gjennom alle detaljer og se mulige
svake punkter. Hvilket utstyr som passer er ikke alltid like lett å vurdere, det kan være
overlappende faktorer der noe er viktig for en, men ikke for andre. Det kan være snakk om
støy, størrelse, eksplosjonssoner, fremtidig ønske om utvidelse eller lignende.
Vakuum
Teorien i et vakuum transportsystem er den samme som for et anlegg som benytter blåseluft.
Vi har et større trykk der vi leder inn materialet og det ender på det punktet hvor trykket er
lavest. Vi trenger å vite alt om materialet, vi må vite ønsket kapasitet og det må bestemmes
hvor rørgaten skal gå. Vi må også vite hvor eventuelle bend kommer. Videre så må vi definere starthastigheten ut ifra partikkelstørrelse, vi må vite bulk og partikkelvekt og om det
er spesielle hensyn å ta i forhold til om materialet. Det er dog noen spesielle forskjeller.
I og med at maskinen vi benytter er plassert i enden så er det viktig at vi har en god
utskillelse i mottaket og ved suger i form av filter. Vi må også ha filtrering foran innsuget der
vi mater inn materialet. Disse tre filtrene gir ekstra trykkfall i rørgaten som stjeler litt kW.
Videre så vil vi også ikke så lett kunne se eventuelle lekkasjer da vi «suger» inn i røret,
kommer det falskluft inn så vil det redusere kapasiteten på anlegget og vi kan måtte jobbe litt
for å finne feilen.
Når vi beregner nødvendig starthastighet og trykkfall så er jobben vi beregner ikke der
vakuumsugeren står. Luften er atmosfærisk der vi mater inn materialet, etter hvert som den
nærmer seg enden og pumpen så synker trykket. Her får vi som for et blåseanlegg en
økende lufthastighet mot enden av røret. Når vi kalkulerer så må vi legge til forventet trykkfall
i mottakssyklonen, filter montert på innsuget til pumpen og filter ved innmating av materiale.
Disse tre trykkfallene vil påvirke lufthastigheten direkte, når tapet øker så synker
lufthastigheten på startpunktet der vi mater inn og vice versa. På grunn av dette så er det
veldig viktig å ha kontroll.
I mottakssyklonen så er det viktig at filteroverflaten er stor nok for å separere ut støvet som
kommer uten for mye tap. Vi beregner dette til en gitt størrelse per m3 luft/min ved
atmosfærisk trykk. Det betyr at om trykket i mottakssyklonen er på 0,5 bar så kan vi halvere
overflaten. Videre så må det utformes med automatisk rens, normalt gjort ved å «skyte»
trykkluft i retur gjennom filterpatronene. «Skytingen» kan settes med intervall fra f. eks 5 til
120 sekunder. Filter foran vakuumsuger og startpunkt har normalt ingen rensefunksjon, det
må byttes ved oppnådd maks trykkfall.
I og med at vi henter luften fra rommet så vil ikke transportluften bli varmet opp, vi har derfor
den fordelen at vi ikke trenger å tenke på varmeutvikling. Vi trenger heller ikke tenke
nevneverdig på at temperaturen kan påvirke materialet utenom ved spesielle situasjoner. Er
f. eks luften kald og mediet varmt så vil det kondensere, vann inn i rørgaten vil ikke være
fordelaktig.
Man bør også tenke på at vakuum kan skape undertrykk i rommet der luften suges inn, det
må være god ventilasjon inn.
I et vakuum anlegg så har vi teoretisk bare trykk fra atmosfærisk og ned til absolutt vakuum å
gå på, dvs minus 1 bar. I et trykkanlegg så kan vi i teorien gå veldig mye lengre – men med
motsatt fortegn. Det vanlige benyttelsesområde i et vakuum anlegg er ned til 0,5 bar. Det
betyr at vi ikke kan ha for langt rørstrekke grunnet trykkfallet som oppstår. Men vi har
muligheten her som for et trykkanlegg å «steppe opp» røret for å redusere trykkfallet.
Det er lett å tenke at når man benytter vakuum så vil systemet bruke mindre kilowatt for å
utføre en jobb. I teorien så er det riktig for det som skjer i rørgaten sin del. Kraften kommer
fra omgivelsene, det atmosfæriske trykket presser luften inn. For pumpen derimot så må den
komprimere luften som suges inn opp til atmosfærisk for å få den ut, jo lavere vakuum vi har
jo mere vil maskinen måtte komprimere – og dessverre trenge kraft. Strømforbruket vil være
der.
Eksempel på pneumatisk transport – vakuum